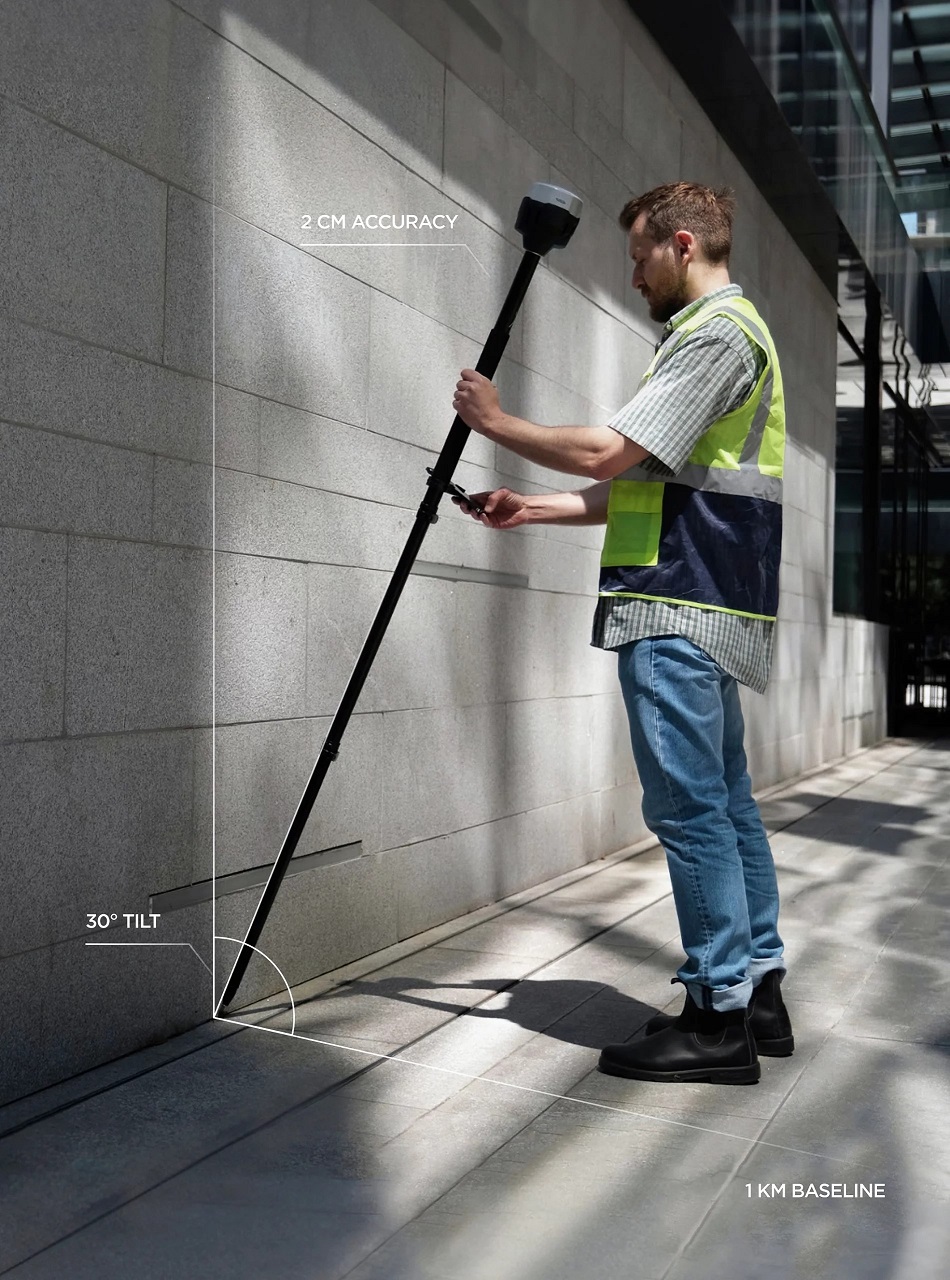
Mining operations have always demanded advanced technologies to ensure safety, accuracy, and efficiency in their inspections. In recent years, the integration of Global Navigation Satellite Systems (GNSS) and Inertial Measurement Units (IMU) has revolutionized the way mining inspections are conducted, offering enhanced precision and real-time data insights.
How do GNSS and IMU technologies enhance mining inspections?
GNSS technology plays a pivotal role in mining inspections by providing precise location tracking capabilities. By leveraging signals from a network of satellites, GNSS enables mining operators to accurately pinpoint the location of equipment, personnel, and geological features, facilitating better decision-making and operational efficiency.
On the other hand, IMU technology can compensate for tilting GNSS receivers and contribute to mining inspections by allowing safe and accurate data collection in hard-to-reach spots of the pit mine, when GNSS equipment can’t be leveled on the required point.
When GNSS and IMU technologies are integrated, they synergize to provide comprehensive insights for mining applications. The combination enables real-time tracking of equipment and personnel, enhances operational safety, and improves overall productivity in mining inspections.
What are the challenges in implementing high precision receivers in mining inspections?
Despite the significant benefits they offer, high precision receivers face operational limitations in underground mining environments. The presence of rock formations and limited satellite visibility can impede the effectiveness of GNSS technology, posing a challenge in maintaining continuous location tracking.
Another challenge lies in data integration and compatibility issues. Mining operations often utilize diverse systems and software for inspections, and ensuring seamless integration of GNSS and IMU data streams with existing platforms can be complex.
Cost considerations also emerge as a factor in implementing advanced technologies. While high precision receivers offer significant advantages, the initial investment and ongoing maintenance costs may pose financial challenges for mining companies, especially in a competitive industry landscape.
How are high precision receivers revolutionizing safety measures in mining?
High precision receivers are driving substantial improvements in safety measures within mining operations. Their integration enables enhanced hazard identification and avoidance by providing accurate location and motion data, allowing mining personnel to recognize potential risks and take proactive measures to mitigate them.
Real-time monitoring of equipment and personnel is another crucial safety aspect supported by high precision receivers. With continuous tracking and data collection, mining operators can ensure the well-being of personnel and the operational efficiency of machinery, contributing to a safer working environment.
What are the key considerations for selecting high precision receivers for mining applications?
When choosing high precision receivers for mining applications, robustness and durability are paramount considerations. These technologies must withstand the harsh and challenging conditions prevalent in mining environments, including exposure to dust, moisture, and mechanical vibrations.
Compatibility with existing mining inspection systems is essential for seamless integration and optimal utilization of GNSS and IMU technologies. Ensuring that high precision GNSS IMU receivers can interface with the current infrastructure and software solutions is critical for efficient implementation.
Scalability for future technological advancements is also a key consideration. As mining operations evolve and incorporate new innovations, high precision receivers should be designed to adapt and integrate with upcoming technologies, ensuring long-term relevance and value for mining companies.
How do high precision receivers contribute to efficiency and productivity in mining inspections?
High precision receivers significantly contribute to efficiency and productivity in mining inspections by streamlining data collection and analysis processes. The accurate and comprehensive data provided by GNSS and IMU technologies enhances the speed and accuracy of inspection activities, optimizing operational workflows.
Furthermore, these technologies aid in optimizing resource allocation and utilization within mining operations. By monitoring equipment and personnel in real time, mining companies can strategically deploy resources and manpower, reducing downtime and maximizing productivity.
Ultimately, high precision receivers support improved decision-making in mining inspections through the delivery of accurate and reliable data. This data empowers mining operators to make informed choices, identify operational inefficiencies, and implement targeted improvements, driving overall performance and sustainability.